Banjo Fittings: Essential Components for Efficient Fluid Transfer
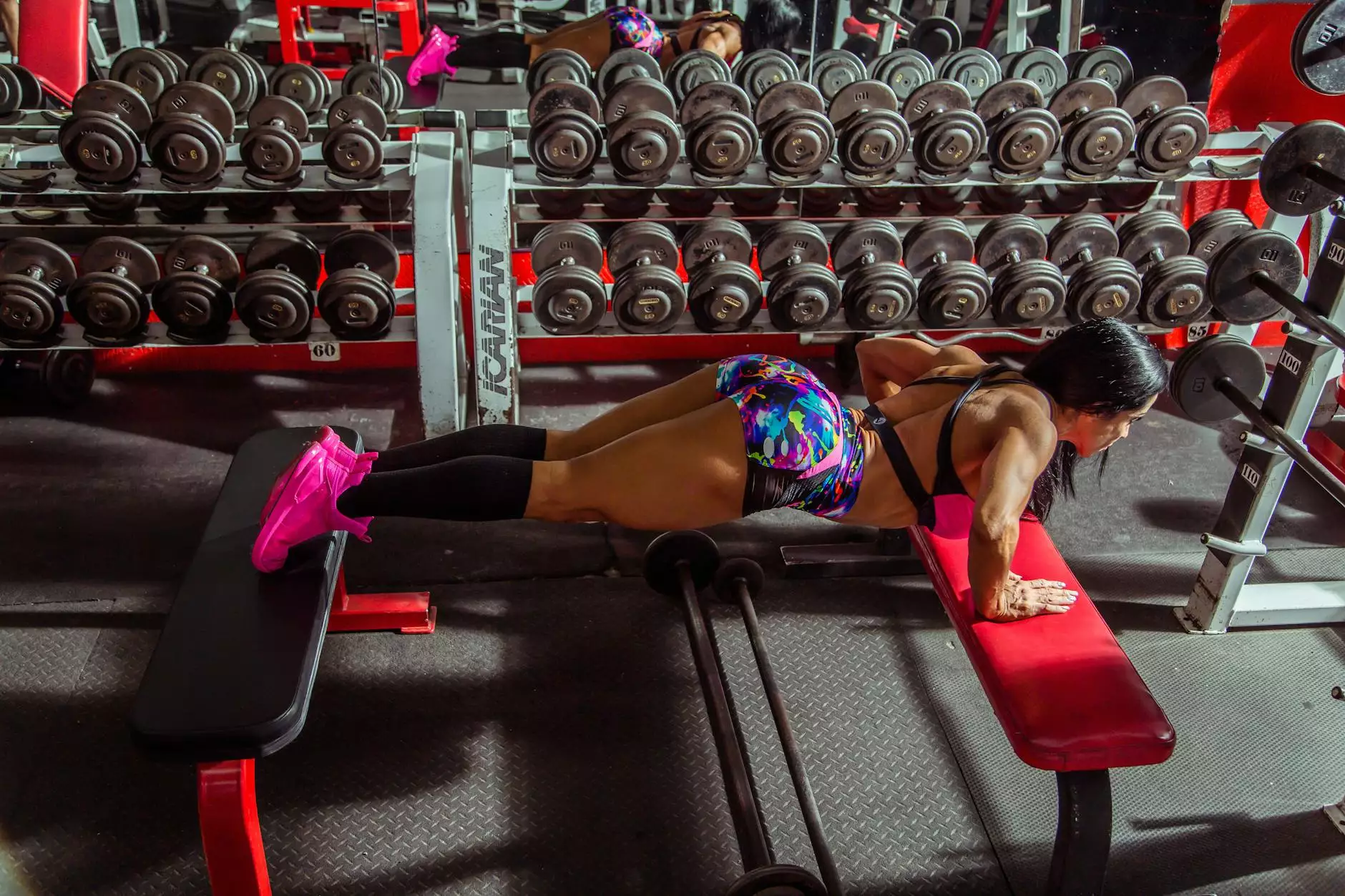
In the world of fluid transfer systems, banjo fittings have emerged as a crucial component that ensures efficiency and reliability. Whether in automotive applications, industrial machinery, or hydraulic systems, these fittings play a vital role in maintaining optimal fluid flows. In this comprehensive guide, we will explore the intricacies of banjo fittings, their applications, benefits, and how they integrate with various systems.
What are Banjo Fittings?
Banjo fittings are specialized connectors used in piping systems to enable the transfer of fluids in a streamlined manner. Characterized by their unique design, these fittings consist of a hollow screw or bolt that connects to a banjo-shaped fitting, allowing for the direct passage of fluids. The primary advantage is their ability to facilitate connections in tight spaces where traditional fittings might be impractical.
Key Features of Banjo Fittings
Understanding the key features of banjo fittings can help you choose the right type for your application:
- Compact Design: The banjo fitting’s design allows it to operate in confined spaces, making it ideal for installations in tight quarters where space is limited.
- Versatile Material Options: Banjo fittings can be made from various materials, including stainless steel, brass, and plastic, allowing for use in different environments and applications.
- Easy Installation: These fittings are straightforward to install, often requiring simple hand tools, which can save time and labor costs.
- Resistant to Corrosion: Depending on the material, many banjo fittings possess a natural resistance to corrosion, ensuring longevity and reliability.
- Leak-proof Connections: When properly installed, they create a secure, leak-proof connection that minimizes fluid loss.
Applications of Banjo Fittings
Banjo fittings find utility in a myriad of applications across various industries. Here are some notable examples:
Automotive Applications
In the automotive industry, banjo fittings are frequently used in brake lines, fuel systems, and coolant lines. Their compact design allows for efficient routing of fluids, which is vital for the performance and safety of vehicles.
Hydraulic Systems
In hydraulic applications, these fittings are commonplace in hydraulic hoses and cylinders. Their ability to withstand high pressure while maintaining a tight seal is crucial for the reliable operation of hydraulic machinery.
Industrial Equipment
Banjo fittings are utilized in various industrial machines, from agricultural equipment to manufacturing systems. They play a role in fluid transfer between components, contributing to overall system efficiency.
Medical Devices
In the medical field, banjo fittings are often used in fluid transfer systems such as IV lines and dialysis machines, where precision and reliability are paramount.
Benefits of Using Banjo Fittings
The adoption of banjo fittings can offer significant benefits that improve the performance and longevity of fluid transfer systems:
- Efficient Fluid Flow: The design of banjo fittings allows for smooth fluid flow, reducing pressure drops and optimizing system performance.
- Space-Saving Design: Their compact nature is ideal for modern, space-constrained applications, facilitating innovative designs.
- Cost-Effective: With easy installation and reduced need for additional fittings, banjo fittings can lead to lower overall project costs.
- Durability: Many banjo fittings are designed to endure harsh environmental conditions, again ensuring reliability and longer service life.
Choosing the Right Banjo Fittings
Selecting the correct banjo fittings for your application involves considering several factors:
Material Selection
The material of the fitting should align with the demands of the application. Stainless steel is often chosen for its strength and corrosion resistance, while brass may be preferred for its cost-effectiveness in low-pressure applications.
Pressure Ratings
Understanding the pressure requirements of your system is vital. Ensure that the banjo fittings you select can handle the maximum pressure your application will experience.
Size Compatibility
Measure and verify the size requirements against the specifications of the components with which the fittings will be used. Mismatched sizes can lead to leaks or system failures.
Installation Tips for Banjo Fittings
To ensure optimal performance and longevity of your banjo fittings, follow these installation tips:
- Clean Surfaces: Ensure that all connecting surfaces are clean and free of debris before installation to achieve a tight seal.
- Tighten Properly: Use the correct tools and follow manufacturer guidelines for tightening the fittings to prevent leaks.
- Inspect Regularly: Periodically check for signs of wear or leaks and replace fittings as needed to maintain system integrity.
Common Issues and Troubleshooting
Despite their reliability, banjo fittings can encounter issues. Here’s how to troubleshoot common problems:
Leaking Fittings
If you notice a leak, check for the following:
- Improper installation or tightness.
- Worn O-rings or seals.
- Corrosion or damage to the fitting itself.
Addressing these issues promptly can prevent further damage to the fluid transfer system.
Pressure Drop
A significant pressure drop may indicate blockages or a mismatch in fitting sizes. Inspect the entire line for obstructions and ensure that all fittings and hoses are appropriately sized.
Understanding Banjo Fitting Specifications
When examining banjo fittings, it’s essential to understand their specifications, including:
Thread Type
Different types of threads (e.g., NPT, JIC) can affect compatibility with other components of a fluid transfer system. Ensure that your fitting matches the thread type of your existing setup.
Working Temperature
Different materials have varying temperature tolerances. Confirm that the selected fittings can handle the temperatures they will be exposed to without degrading.
Flow Rate
Evaluate the flow rate of your application. The design and size of the banjo fittings should support the expected flow rates to prevent bottlenecks.
Maintaining Your Banjo Fittings
To maximize the lifespan and performance of your banjo fittings, regular maintenance is necessary. Here are practical tips:
- Routine Inspections: Establish a regular schedule for inspecting fittings for wear, corrosion, or leaks.
- Replacement of Worn Parts: Proactively replace O-rings, seals, and fittings that show signs of wear.
- Debris Removal: Keep the surrounding area clean and free of debris that may interfere with connections.
Conclusion: The Importance of Banjo Fittings in Modern Systems
In conclusion, banjo fittings are indispensable elements in fluid transfer systems across multiple industries. Their unique design, ease of use, and reliability make them an excellent option for various applications. By understanding their features, benefits, and proper maintenance, you can enhance your projects, improve system performance, and ensure safer operations.
For high-quality fittings, visit fitsch.cn to explore our range of fittings for sale and elevate your fluid transfer solutions today!