Understanding the Landscape of Plastic Molding Manufacturers
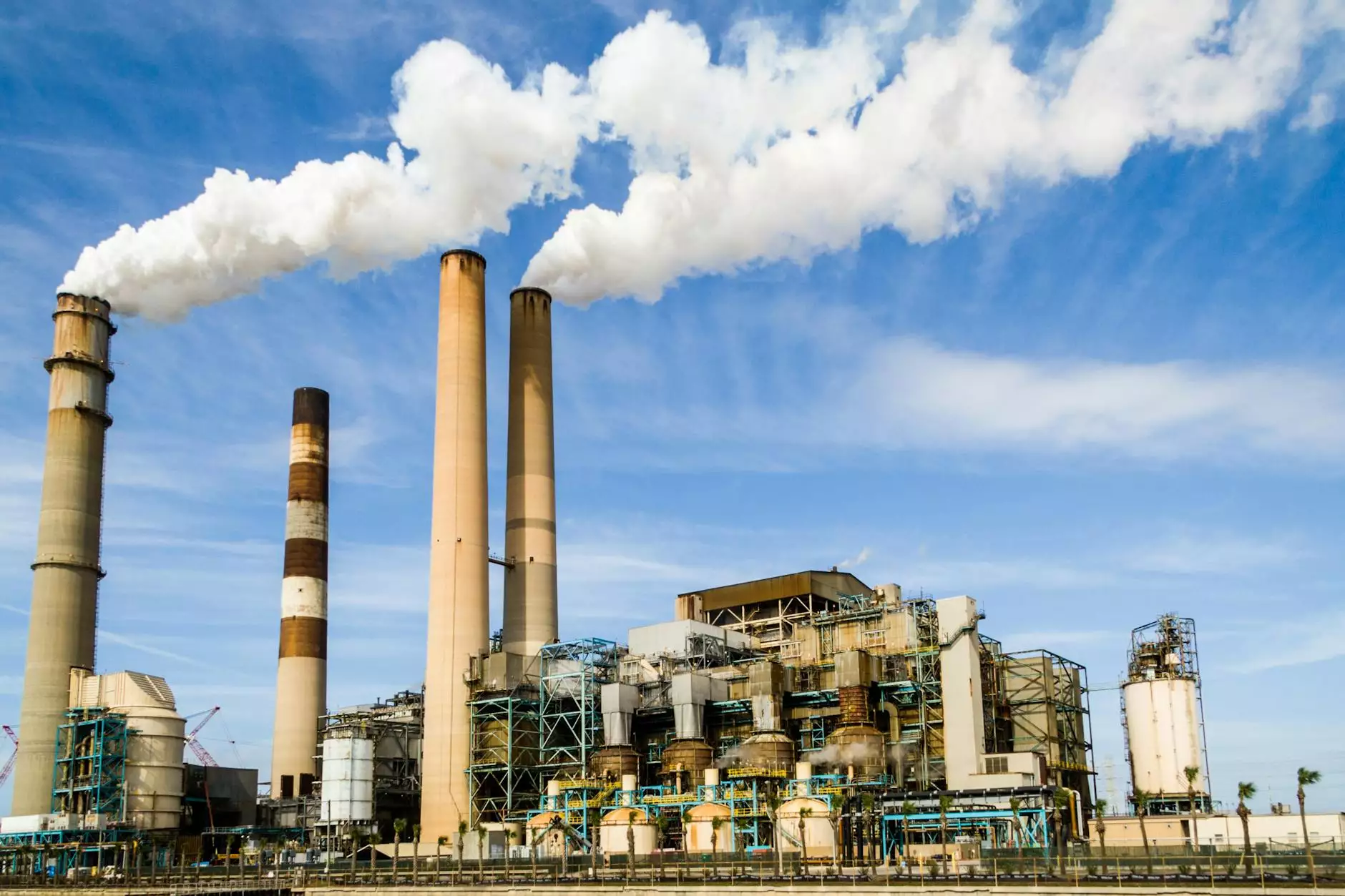
In the modern manufacturing ecosystem, plastic molding manufacturers play a pivotal role in supplying the essential components required by various industries. This article delves into the intricacies of the plastic molding process, the types of molding techniques, and the leading figures in the industry, including established companies like DeepMould.
The Importance of Plastic Molding
Plastic molding is a critical process that allows for the creation of a myriad of products. From automotive parts to household appliances, the versatility of molded plastics is unparalleled.
Why Choose Plastic Molding?
- Cost-Effectiveness: Plastic molding is typically more affordable than other manufacturing methods.
- Design Flexibility: It allows for complex shapes and designs that can be difficult or expensive to achieve through other methods.
- Production Efficiency: Molding is capable of producing large volumes in a relatively short amount of time.
- Material Variety: Manufacturers have a wide range of materials to choose from, including thermoplastics and thermosetting plastics.
Types of Plastic Molding Processes
Understanding the different types of plastic molding processes can help businesses choose the right method for their product needs. Here are some of the most common methods used by plastic molding manufacturers:
1. Injection Molding
Injection molding is one of the most widely used processes in the plastic manufacturing industry. In this method, plastic pellets are heated until they melt and are then injected into a mold. The ability to create complex shapes with high precision makes this method a favorite among manufacturers.
2. Blow Molding
Utilized mainly for hollow plastic products, blow molding involves inflating hot plastic inside a mold. This technique is particularly advantageous for producing bottles and containers.
3. Compression Molding
Compression molding involves placing a plastic material in a heated mold, where it is compressed to form the desired shape. This method is commonly used for large parts, such as automotive bumpers and kitchen countertop sinks.
4. Rotational Molding
This process is specifically useful for creating large, hollow objects. The mold is rotated on an axis to allow the plastic to coat the interior evenly, making it ideal for items such as kayaks and storage tanks.
Key Considerations When Working with Plastic Molding Manufacturers
When partnering with plastic molding manufacturers, there are several critical factors to consider:
1. Material Selection
The choice of material significantly affects the product’s performance. Factors such as strength, flexibility, and temperature resistance must be taken into account. Common choices include:
- Polyethylene (PE)
- Polypropylene (PP)
- Polyvinyl Chloride (PVC)
- Polystyrene (PS)
2. Design and Prototyping
Effective design is crucial to the success of the molding process. Utilizing CAD (Computer-Aided Design) and prototyping technologies can help manufacturers visualize the final product, making it easier to make adjustments before production.
3. Production Volume and Scale
Understanding the expected production volume is essential. High-volume production runs may justify the initial investment in custom molds while lower volumes might benefit from less expensive options.
4. Quality Control
Quality assurance is vital in ensuring that the final products meet industry standards and customer expectations. Working with manufacturers that adhere to stringent quality control processes can mitigate risks.
Challenges Faced by Plastic Molding Manufacturers
While the plastic molding industry offers numerous advantages, manufacturers must navigate certain challenges:
1. Environmental Concerns
The production and use of plastics raise significant environmental questions. Manufacturers are increasingly looking for sustainable practices, including recycling and using biodegradable materials.
2. Supply Chain Disruptions
Global events have shown that supply chain issues can impact the availability of raw materials. Manufacturers must stay agile and have contingency plans in place.
3. Rising Production Costs
Fluctuations in the prices of raw materials can affect production costs. Manufacturers must find ways to streamline operations and maximize efficiency.
Leading Plastic Molding Manufacturers
Many companies excel in the field of plastic molding, offering innovative solutions and high-quality products. Some notable names include:
1. DeepMould
As a leading force in the industry, DeepMould specializes in custom plastic molding solutions tailored to various sectors, from automotive to consumer goods.
2. Nypro (A Jabil Company)
Nypro is renowned for its advanced manufacturing capabilities and commitment to sustainability, providing effective molding solutions worldwide.
3. Flextronics
Flextronics combines technology and consumer electronics expertise to provide molding services that cater to a highly dynamic market.
4. Rigid Industries
This company focuses on high-quality molded products with a strong emphasis on customer service and timely delivery.
The Future of Plastic Molding Manufacturing
As we look ahead, the plastic molding industry will continue to evolve. Here are some trends shaping its future:
1. Advancements in 3D Printing
3D printing technology is making waves in the molding industry, allowing manufacturers to create complex prototypes quickly and cost-effectively.
2. Increasing Demand for Sustainable Practices
With growing regulatory pressures and consumer demand for sustainable products, manufacturers are looking to integrate recycled materials into their processes.
3. Smart Manufacturing Technologies
Automation and IoT (Internet of Things) will play an increasing role in enhancing productivity and reducing costs in the plastic molding sector.
Conclusion
In summary, the role of plastic molding manufacturers is vital in powering many sectors of the economy. With ongoing advancements in technology, rising awareness of sustainability, and the importance of quality and efficiency, the future looks bright for companies that are ready to embrace these changes. Leading players like DeepMould are already at the forefront of this evolving landscape, offering innovative solutions to meet the diverse needs of their customers.
As businesses look to outsource their manufacturing needs, understanding the capabilities and advantages of different plastic molding manufacturers will remain crucial. By leveraging the expertise of specialists in this field, companies can optimize their production processes, reduce costs, and ultimately deliver superior products to the market.